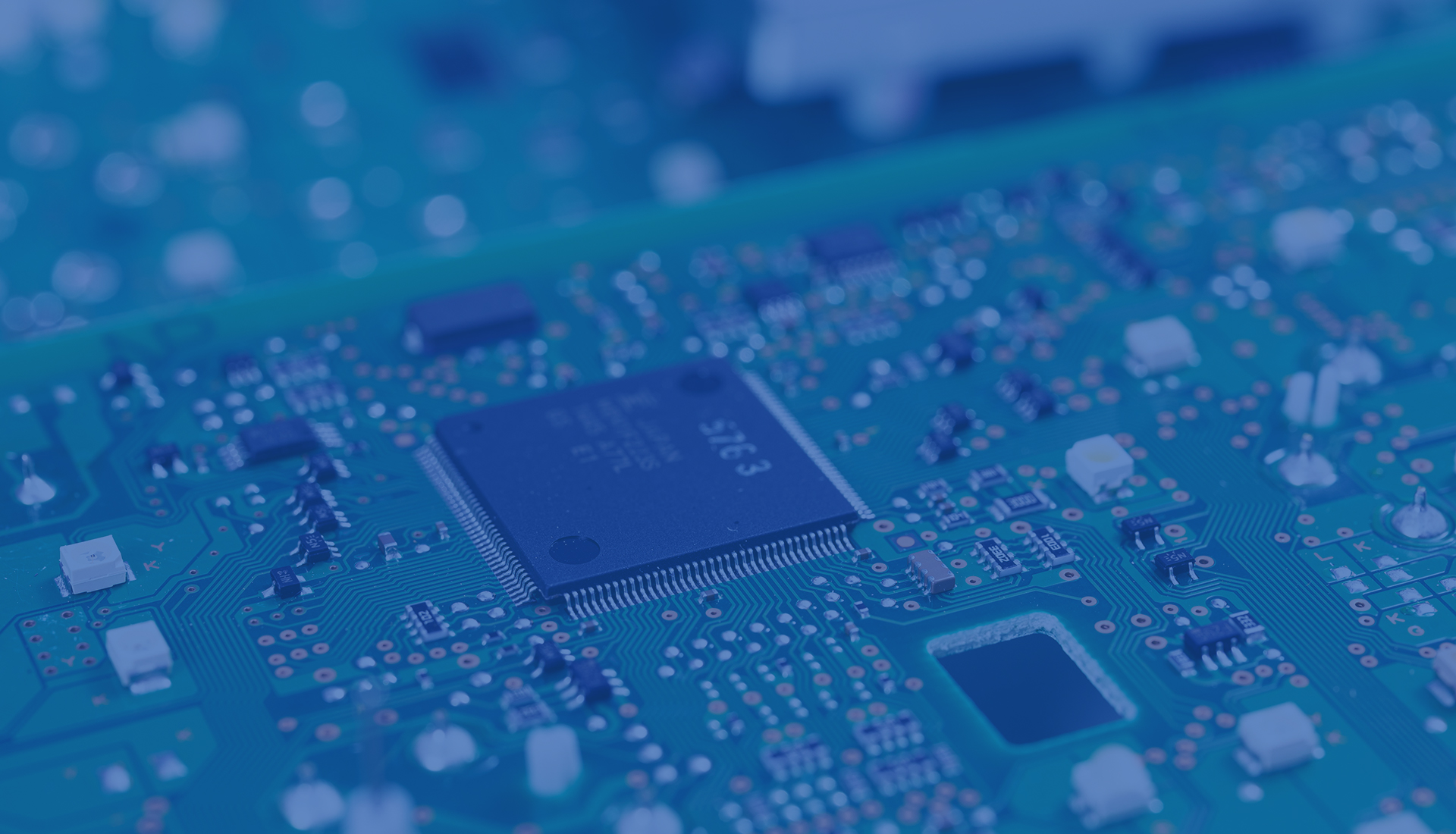
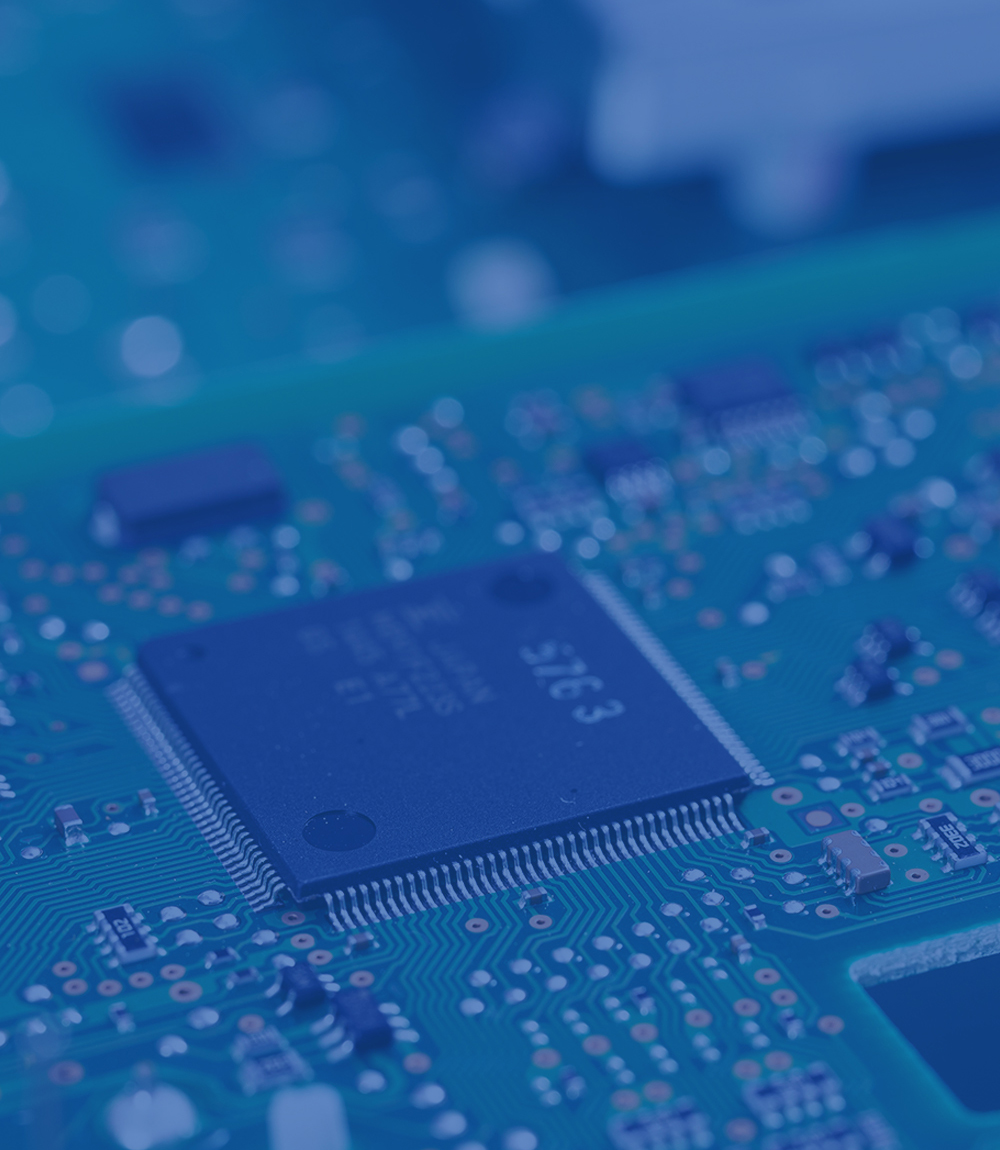
Training
System
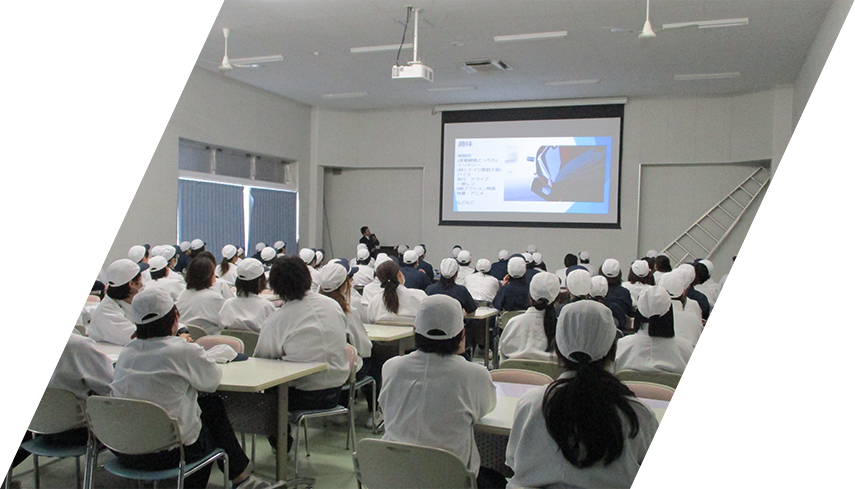
When individual workers grow professionally and personally,
the organization grows.
For a company to grow big, it must have a solid employee development program.
Hokuichi has its own employee training project called Hokuichi Innovated Project (HIP).
We associate the letter “H” in the abbreviation with the word “human”. The program’s goal is to improve
the work environment and productivity by empowering each worker and promoting helping and caring for
each other to grow together.
Employee Development Program
In addition to new employee training, Hokuichi holds various upskill programs with mixed age groups from different work divisions.
New Employee Training
New employees can get an idea and feel about what the company does through various hands-on training sessions.
Work Environment and Productivity Improvement Activity
Hokuichi is engaged in various activities to make itself a better company and place to work.
New Employee Training
Hokuichi’s new employee training is unique because all new employees have the chance to work in all
sections to gain a comprehensive idea of what kind of work each section does.
This way, new employees can start their careers with a clear idea of what is expected.
Work Environment and Productivity Improvement Committees
Each employee is assigned to one of the three committees, each of which has a different focus, such as
work environment improvement, employee development, and problem solving.
These team activities stand on the idea that employees can make a difference and create an outstanding company.
All employees from across different divisions participate in each of the following three committees.
6S Committees
Ensure that the work environment is kept clean and efficiently organized for all employees to feel comfortable to working.
No.1 Committees
Help each employee attain an ideal professional life where they set goals, enjoy what they do, and advance professionally.
HELP Committees
Identify issues at the workplace, address them, and develop problem solving skills collectively.
6S Committees
Hokuichi is a firm believer of the 6S lean management methodology, which contains the following 6 Japanese words: Seiri [sort], Seiton [straighten], Seiso [shine], Seiketsu[standardize], Shitsuke [sustain], and Setsuyaku [be smart on resources].
We ensure that our workplace is organized and provided with appropriate signs for areas, such as storage.
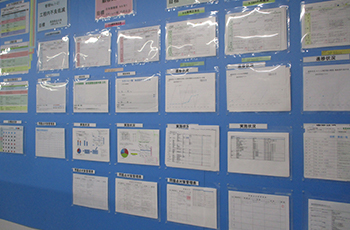
The findings and achievements of committee activities are posted on the wall for members to see and easily understand.
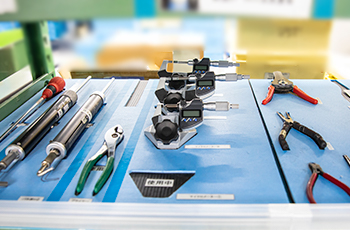
Tools are provided with their own dedicated storage space.
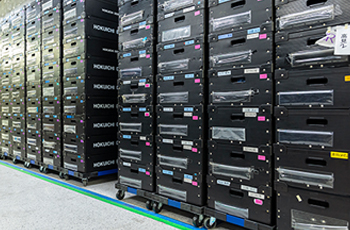
Factory items are kept in an extremely orderly manner; items, their storage area and quantity are all specified.
No.1 Committees
The committee helps employees become “No. 1” by achieving their professional goals. The goals are written on a sheet of paper and posted on the board in the common area. The committee also encourages its employees to follow the “Ten Rules of Hokuichi”.
The Ten Rules of Hokuichi
- Greet with passion.
- Dress properly and use appropriate language.
- Listen intently.
- Be punctual.
- Practice Seiri [sort], Seiton [straighten], Seiso [shine] frequently.
- Practice the “ho-ren-so” communication style.
* The word “horenso” is an abbreviation of three Japanese words: ho [report], ren [contact], and so [consult] that describe the essence of an effective business communication style. - Follow rules.
- Be considerate of others.
- Be a worker hungry for improvement.
- Think with your head, take initiative, and act.
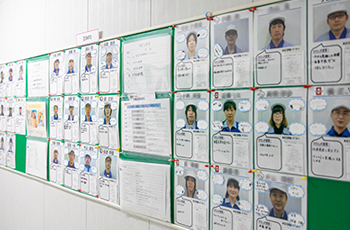
Declare Goals
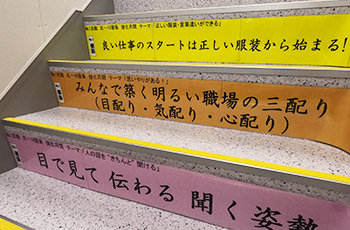
Ten Rules of Hokuichi’s Enhancement Program
HELP Committees
We require each employee to submit a productivity improvement idea once a month. Rewards go to those who provided ideas with high value. We also use this opportunity for those employees who want to escalate critical issues to the managers. Members are given a special system to raise such an alarm called “Help Card”.
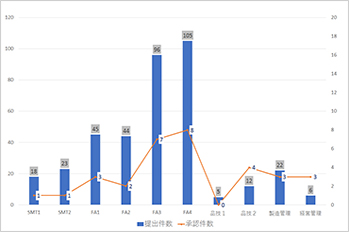
Trend of Idea Submission and Approval Rate
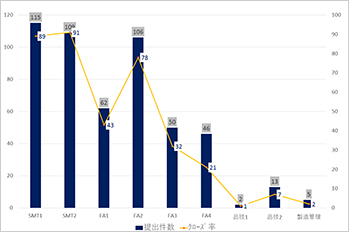
Trend of Help Card Submission and Action Closure
Hokuichi stops the production line once a month to dedicate itself to productivity improvement activities fully. Issues and improvements need to be addressed and solved promptly. Hokuichi defines the production halt day as an opportunity to optimize itself on a regular basis.
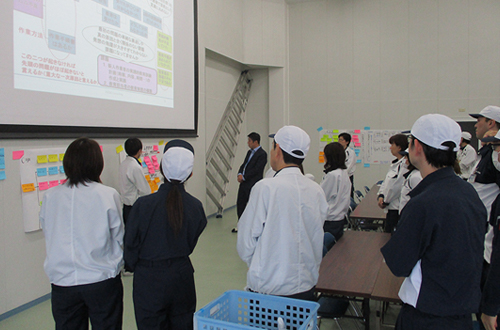
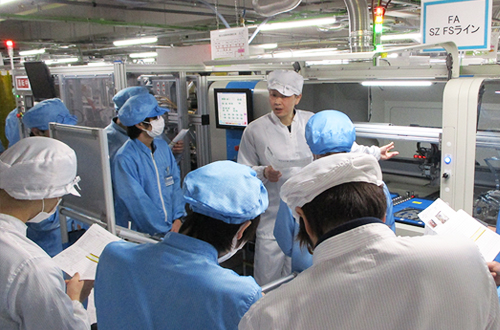